
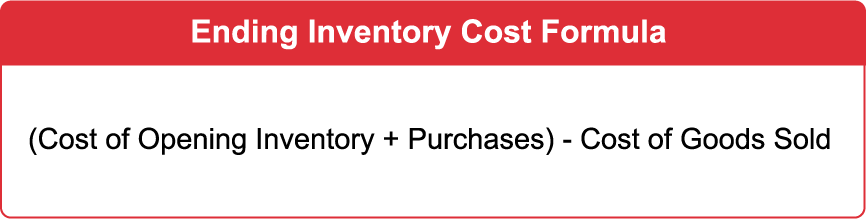
The EOQ formula requires that demand (and lead-time) for a inventory item be constant. Note: This aspect of inventory control produces a few problems. Taking the previous example of the demand in lead-time being 150 units, we’re considering the possibility of demand being more than 150 or less than that. If demand in lead-time varied, it could be described by means of some form of probability distribution. So, if lead-time for a particular inventory item is five days and daily demand is 30 units, the re-order level would be five days at 30 units per day, 150 units. Re-order level (ROL) = Demand in lead-time Specifically, the order should be placed when there is still sufficient inventory to last five days, ie: If the lead-time is, say, five days, an order has to be placed before inventories have been exhausted.

Figure 4 illustrates the problem and its solution. If suppliers take some time to provide goods, orders need to be placed in advance of running out. The assumption of constant demand is consistent with the assumptions underlying the EOQ formula. An organisation could simply wait until it ran out of inventory, click its corporate fingers, and inventory would arrive instantaneously.
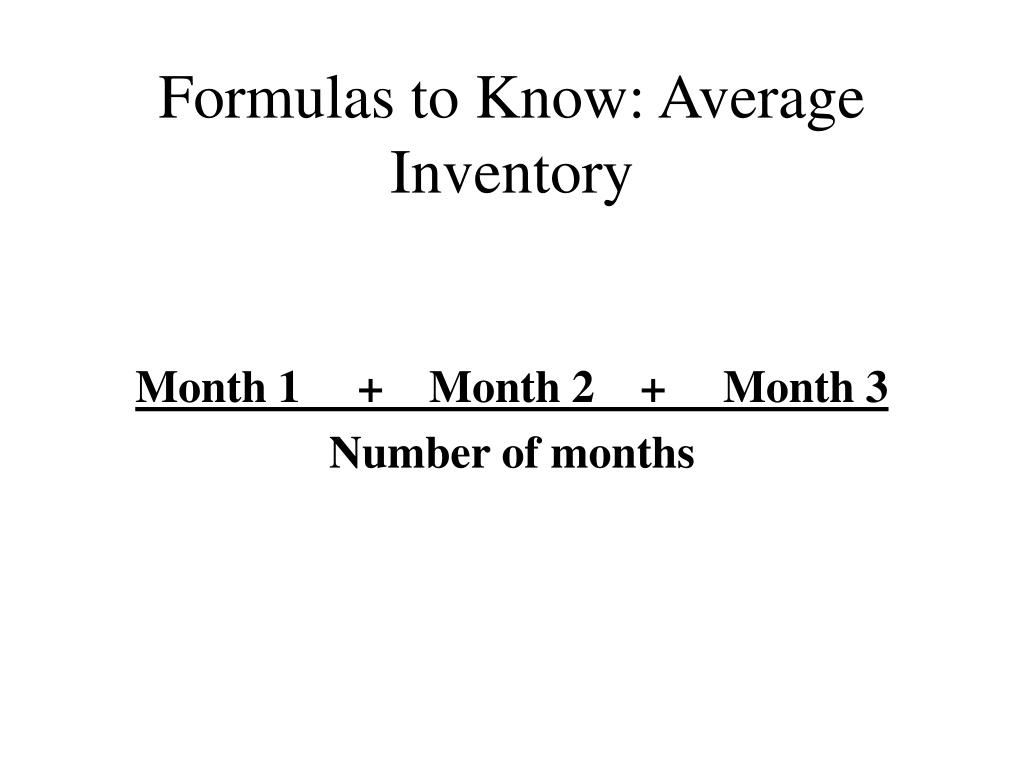
If it were possible, a re-order level of zero could be adopted. It is unlikely that this could be reduced to zero – it would require astonishingly co-operative and efficient suppliers. ‘Lead-time’ is the interval between placing an order with a supplier and that order arriving. When it comes to calculating re-order levels, three sets of circumstances can be envisaged. The re-order level as explained below should not be confused with the inventory control levels referred to in textbooks – this article ignores these. If orders are placed too soon, when there are still substantial supplies in inventory, then inventory levels and holding costs will be unnecessarily high. If an order is placed too late, when inventories have been allowed to run too low, a ‘stock-out’ will occur, resulting in either a loss of production or loss of sales, or possibly both. This involves finding the total annual cost (holding cost, re-ordering cost and purchasing cost) at the level indicated by the EOQ and at the level(s) where discount first becomes available.įigure 3 shows total costs (now including cost of purchasing the inventory) plotted against order quantity with discount incorporated.Īs important as how much to order at a time is the question of when to order more inventory.
#HNEW AVERAGE INVENTORY FORMULA TRIAL#
The common approach is one of trial and error. While prices reduce, total annual holding costs will increase if more inventory is ordered at a time, so the matter needs a little thought. Both holding costs and re-ordering costs should be in $, or both in cents.Ī common twist to exam questions is to ask students to evaluate whether bulk discounts are worth taking. Annual demand and cost of holding a unit for a year.
#HNEW AVERAGE INVENTORY FORMULA PROFESSIONAL#
An introduction to professional insights.Virtual classroom support for learning partners.Becoming an ACCA Approved Learning Partner.
